Hot spotting happens a lot on automotive brake rotors.
In most cases, it will go away after a period of use but if you observe hot-spotting the key thing is “Are you having brake vibration?” – As this may be a by-product of the hot spotting.
Three things can reduce hot spotting
- Getting a matched rotor and pad set. Not all pads have the same scrub factor and not all rotors are made from the same irons. (read below comments on various irons)
- If using a slotted rotor use one with a large enough quantity of grooves or wide enough grooves.
- Allowing the pads time to bed in and following bed-in procedures
Scrub factor (or light abrasion) is how the pad seats itself to the rotor in early life and cleans up the rotor under heat cycling. (We talk about this “scrub factor” first as it allows the rest of the article to make sense).
People shout out about “Low dust” pads but the reality is if you don’t have a certain scrub factor you don’t have a brake and all forms of abrasion cause dust (which is a mixture of disc material and pad materials – see this link ). So a “no dust” pad if anyone could find one… will almost certainly lead to hot spots and possibly shudder.
Cast iron grades. Basically, in the automotive market, there are TWO only. Yes, there are ceramic or carbon ceramic rotors and other non-iron race rotors but these are very expensive and never found on production cars except for a handful of exotics.
We are talking here about 99.5% of all production cars using IRON in its two basic forms;
G3500 High carbon – found on a few German cars from new and very good when used in a balanced match with the OE pads or one with a similar scrub factor. At EBC we use these on our SG2F race rotors. G3500 is more expensive but needs to be used with a matched pad with a matched scrub factor for one simple reason – the carbon will come out of the solution in the rotor under hard braking and that’s what these hot spots are. Use the right pad and the spots will go soon and the brake will be perfect. Why use G3500??? Because it is slightly better at heat absorption and crack resistance under heavy loads.
G3000 Normal Carbon – 95% of all cars use this iron. This is a great material for most brakes on cars, easier to match with pads, and less expensive than G3500
What’s the difference – It’s tiny… generally speaking grey iron rotors with below 3.5% Carbon are G3000 material and above 3.5% they are in the G3500 category.
EBC best matches pad compounds for iron rotors
G3000 iron – Greenstuff, Yellowstuff and Bluestuff all have a scrub factor of 5-6 ( our internal measurement )
G3500 iron – RP1, RPX, SR11 and SR21
So when you buy non-EBC rotors check first which grade of iron you have been supplied, EBC plain, USR, GD, and BSD are all G3000, and EBC two-piece SG2F are all G3500 material.
We have omitted here the new and very attractive EBC SR series sintered race pads, as they work very differently to normal pads by laying down a film deposit on the rotor and actually braking on that film so almost zero rotor wear. SR series are not for street use, they are all out trackpads and are setting the new standards by which all race pads are now being judged.
There are many articles on these subjects but
- There is no such thing as rotor warping – there is only Disc thickness variation caused by a rotor with an excess runout at installation cured only by turning on a Pro Cut on a car brake lathe.
- Don’t confuse hot spots with outline etching where an outline stain of the pad compact appears on the rotors after the vehicle is parked (usually in the wet)
- Don’t look for a zero dust brake pad as these don’t exist – however EBC pads contain zero steel fiber which is present in all other pads so EBC will be lower dust than most and the dust will clean off wheels easier
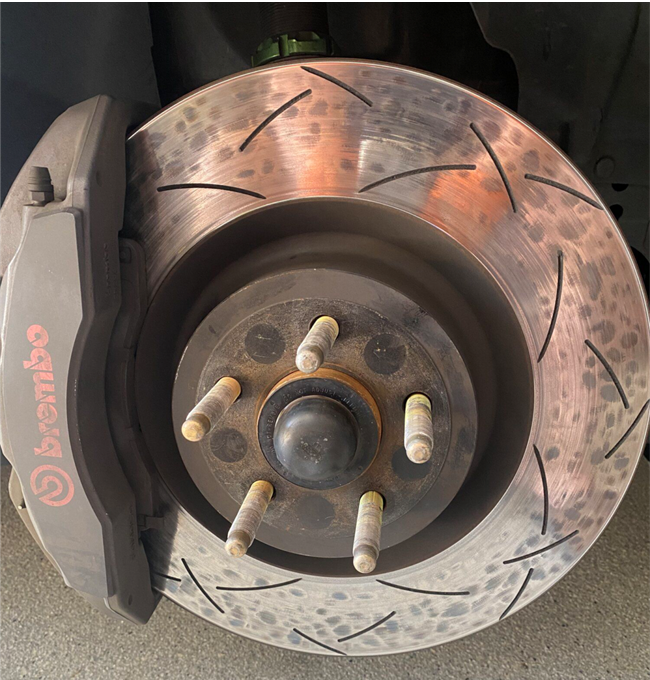